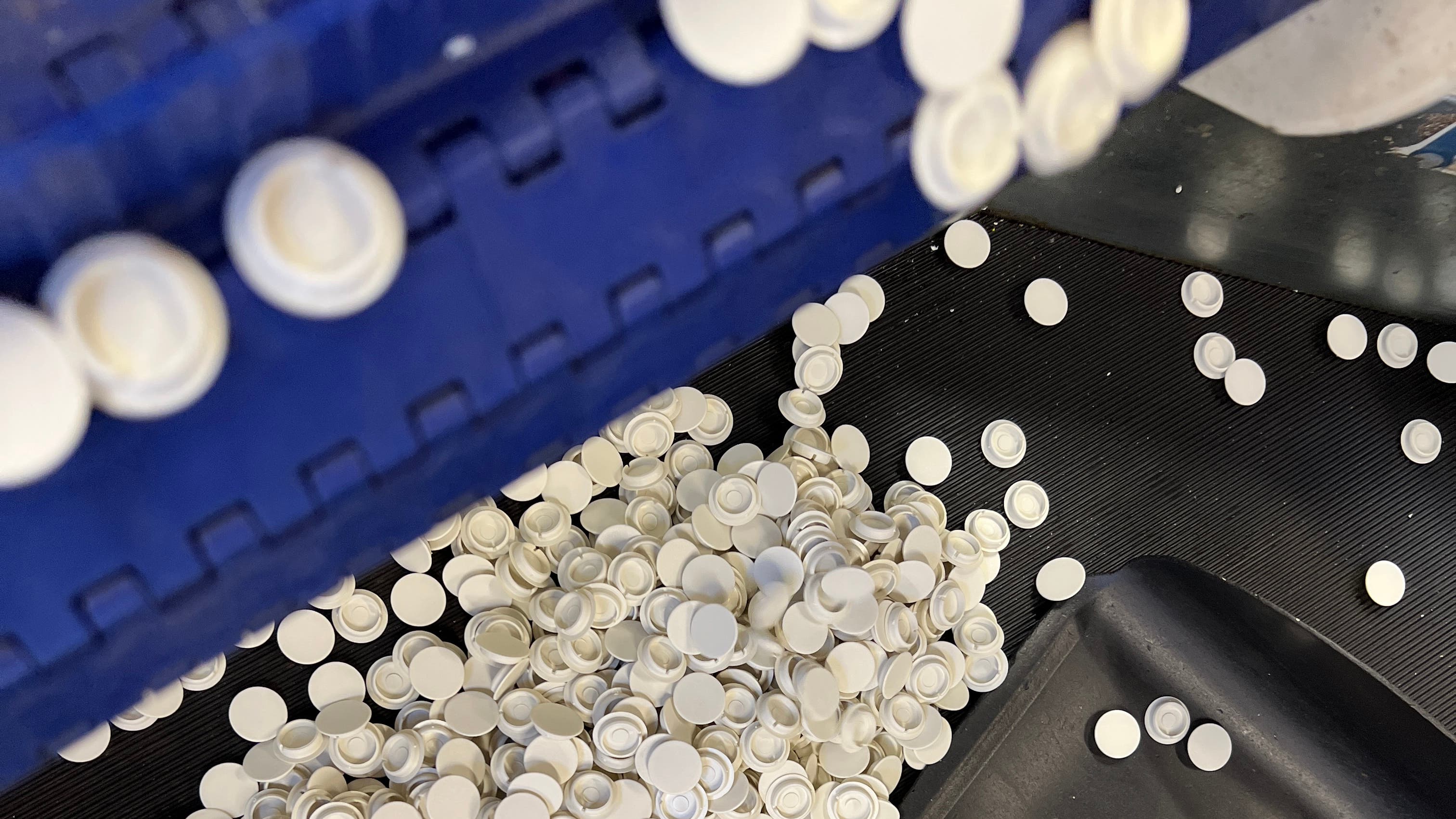
How does it actually work?
Injection molding
- how it works
The production of injection moulded plastic parts requires precisely adjusted machines where our knowledge of the plastic’s properties is very important. Read about how injection moulding works.
Injection moulding - a circular
production process
Proper drying of plastic materials is crucial for achieving optimal properties in injection moulding. Moisture can lead to poor production and unattractive details in furniture components. Each mould undergoes rigorous testing to ensure functionality. The process begins as plastic granules melt in a cylinder, propelled by a rotating screw that pushes the molten plastic forward. This liquefied material is then injected into the mould tool with carefully controlled flow. After cooling, the mould opens to release the finished plastic part. Excess material, known as sprue, is often recycled for future production. Post-moulding, the product requires acclimatization, reabsorbing moisture to attain its intended characteristics. This meticulous process ensures high-quality plastic elements for modern furniture design.
1. Plastic granules 2. Rotating screw 3. Melted plastic 4. Mould 5. Shape of the plastic part
6. Finished plastic parts 7. Sprue/waste material 8. Sprue is ground and returned to the process
Advantages of injection
molded plastic parts
Injection molding is a reliable and cost-effective production method with many advantages, such as creating minimal production waste, providing high efficiency and consistent quality. It is easy to adapt production for both small and large series. Another important advantage of injection molding is the flexibility in terms of materials and colours, making it possible to produce parts in a variety of design variants, even very complex ones. Additionally, granulated recycled material, such as fishing nets, can be reused, making it a more sustainable option.
- Minimal waste
- High efficiency
- Consistent quality
- Flexibility with materials and colours
- Both simple and complex parts
- Sustainable option with recycled plastic material
What do you look for
in a quality control?
In a quality control, you check for shape, sink, flash, and colour. The produced plastic part is compared to a master sample approved by the customer. Most plastic materials shrink within the first day, but it can take several days depending on the material. When manufacturing the tool/mold, we consider how much the specific plastic part to be produced will shrink.
Sink on the plastic part
There is a risk of sink when there are variations in the material’s thickness, and you can minimize the risk or address it by changing the design.
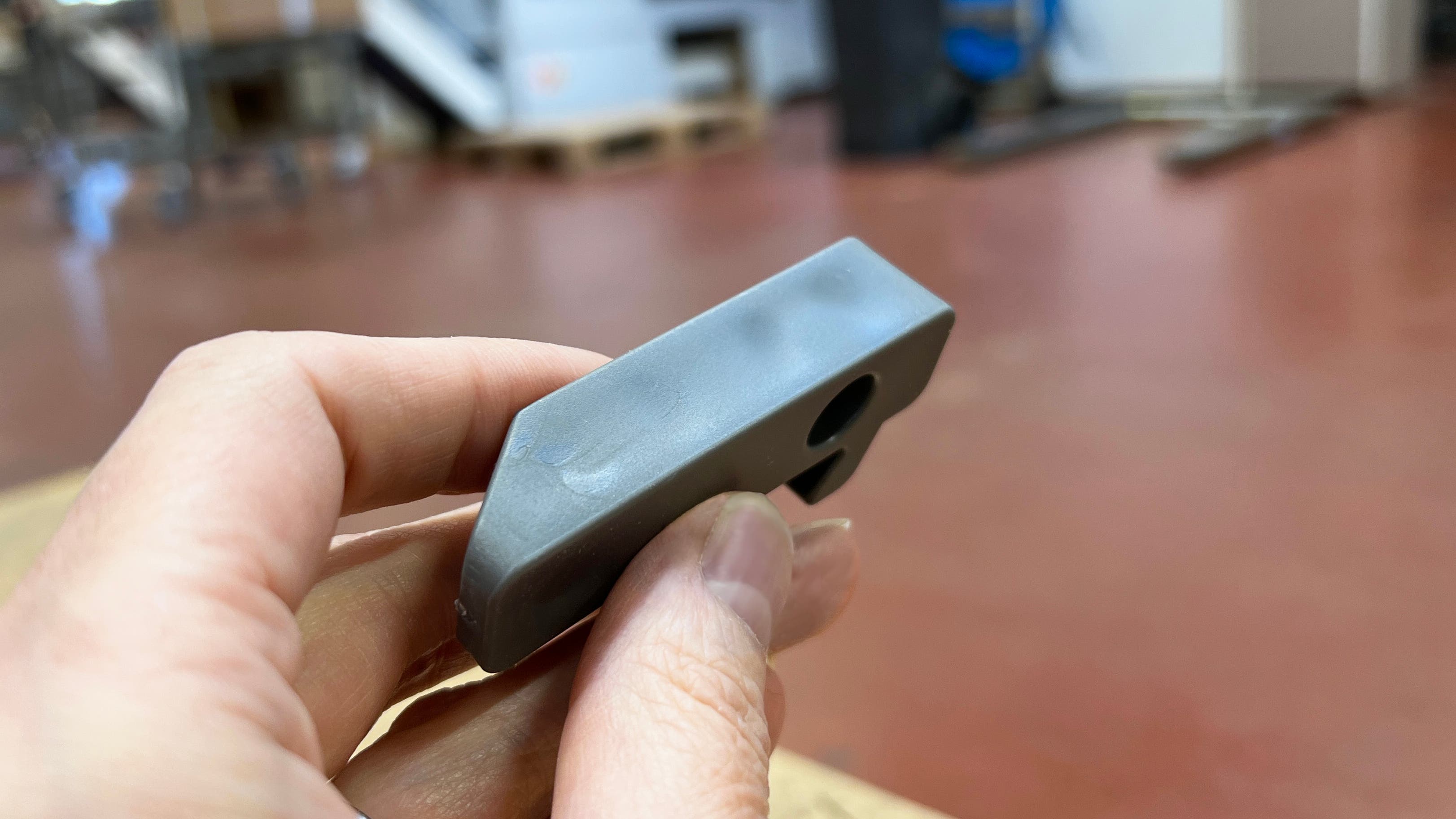
Flash - usually at the parting line
Flash is usually found at the parting line and can be due to temperature, pressure, cooling, or time.
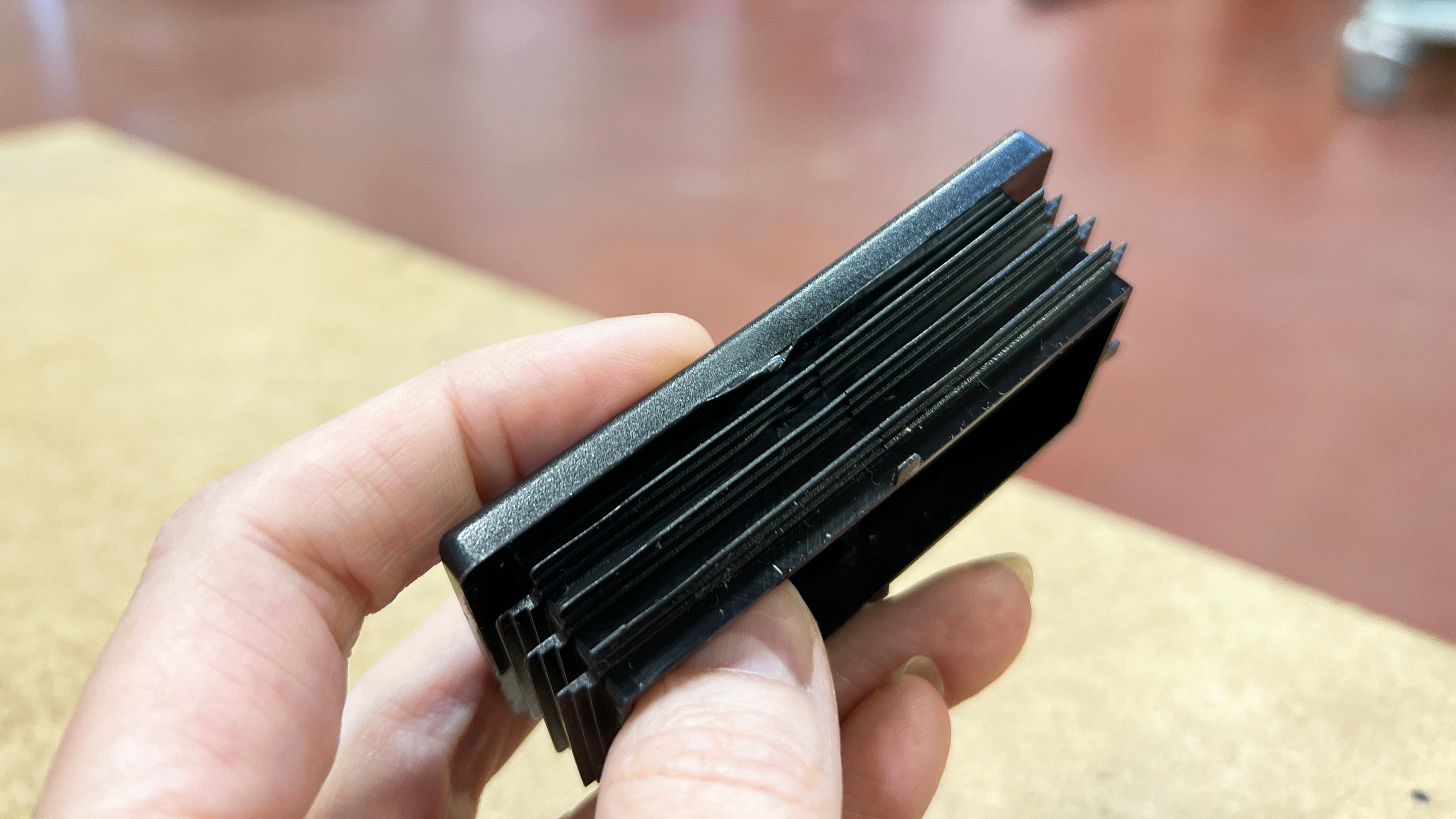
Is the colour of the part correct?
The colour is compared to the master sample. Regarding colour, we plan production to go from light to darker plastic parts to reduce waste. It is sensitive to run white, blue, red, and signal colours, and the machine needs to be thoroughly cleaned before changing colours.
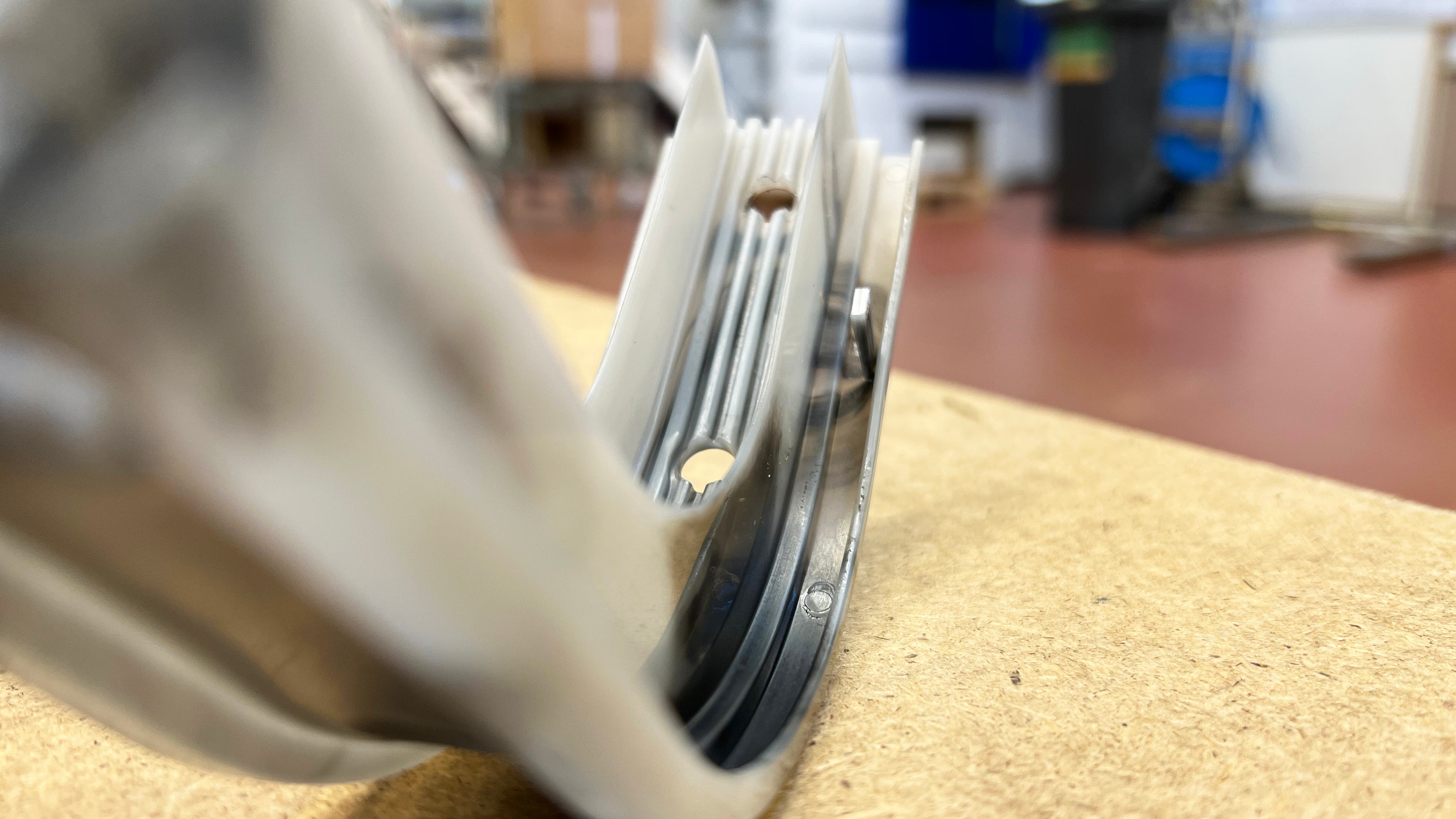
Surface finish and patterns for plastic surfaces
There are many options when it comes to surface finish for injection molded plastic parts. The possibilities are almost endless.
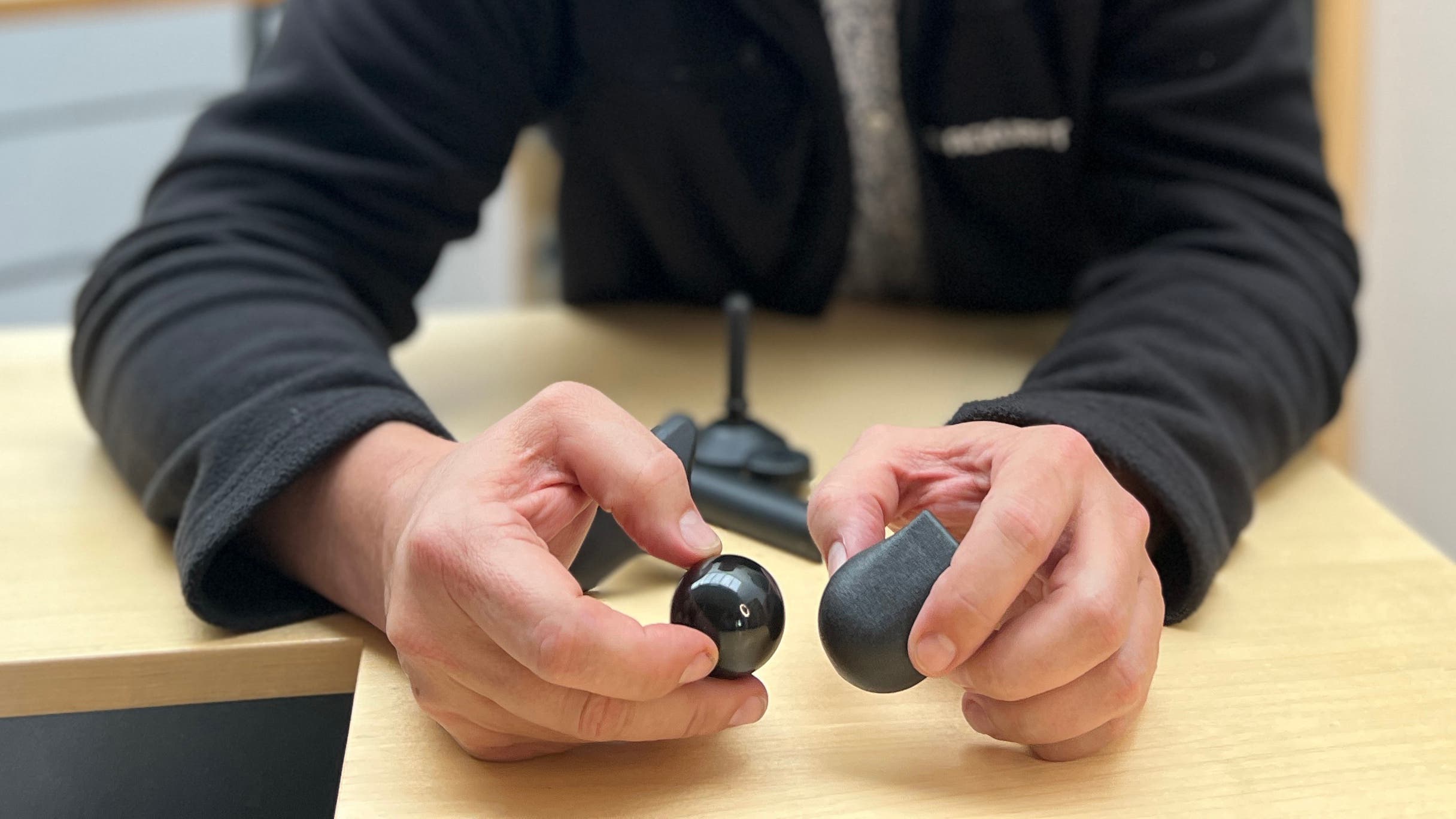
Plastic materials for injection molded plastic parts
When it comes to injection molded plastic, the choice of plastic material is crucial for the result. With the right material, you get a longer product lifespan, increased strength, and better resistance to chemicals. If you need to discuss plastic materials, please contact our product development department.
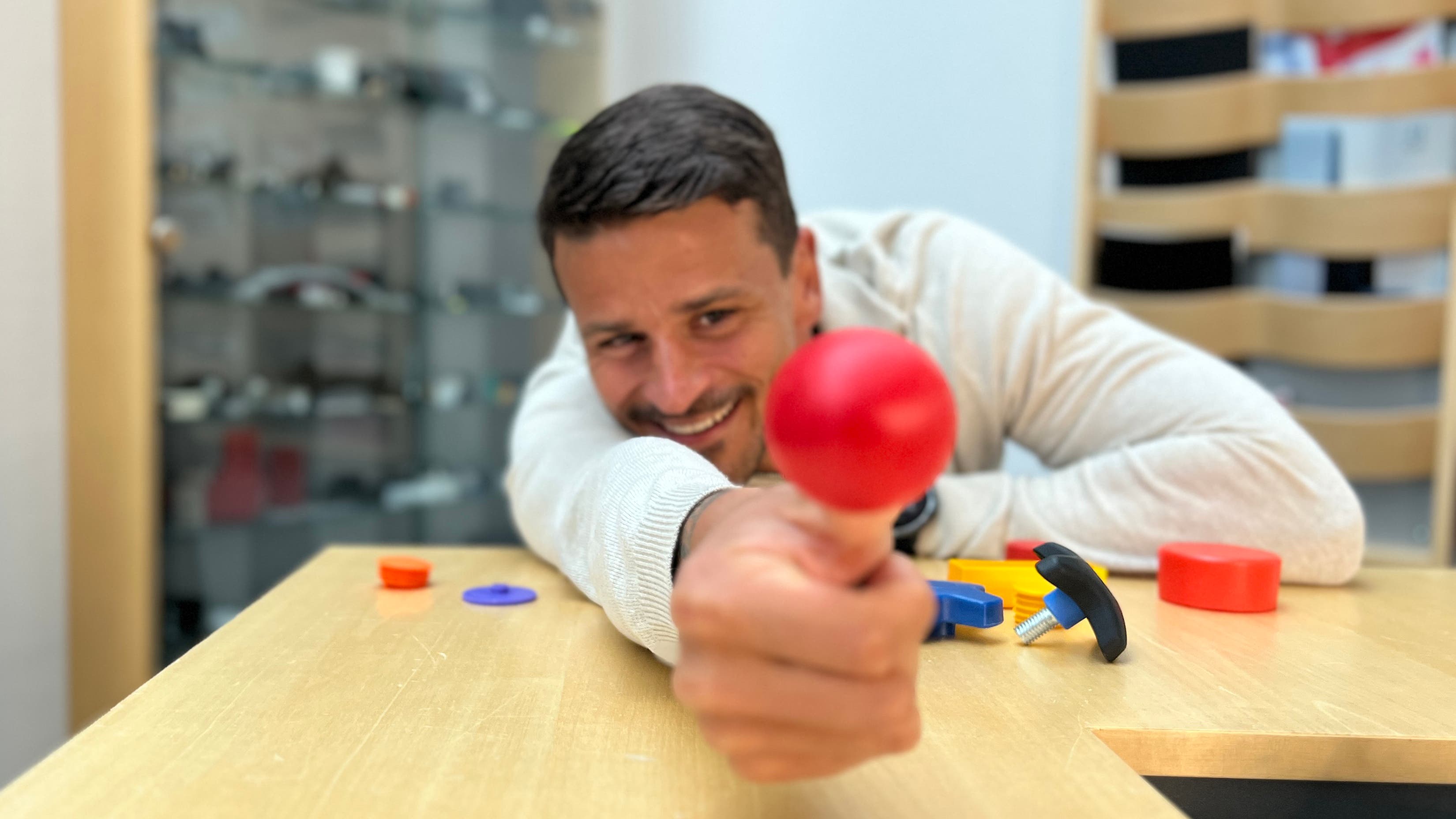
Want to know more about plastic?
Order the book “Worth Knowing About Plastic” from Polymercentrum.
Available in English.
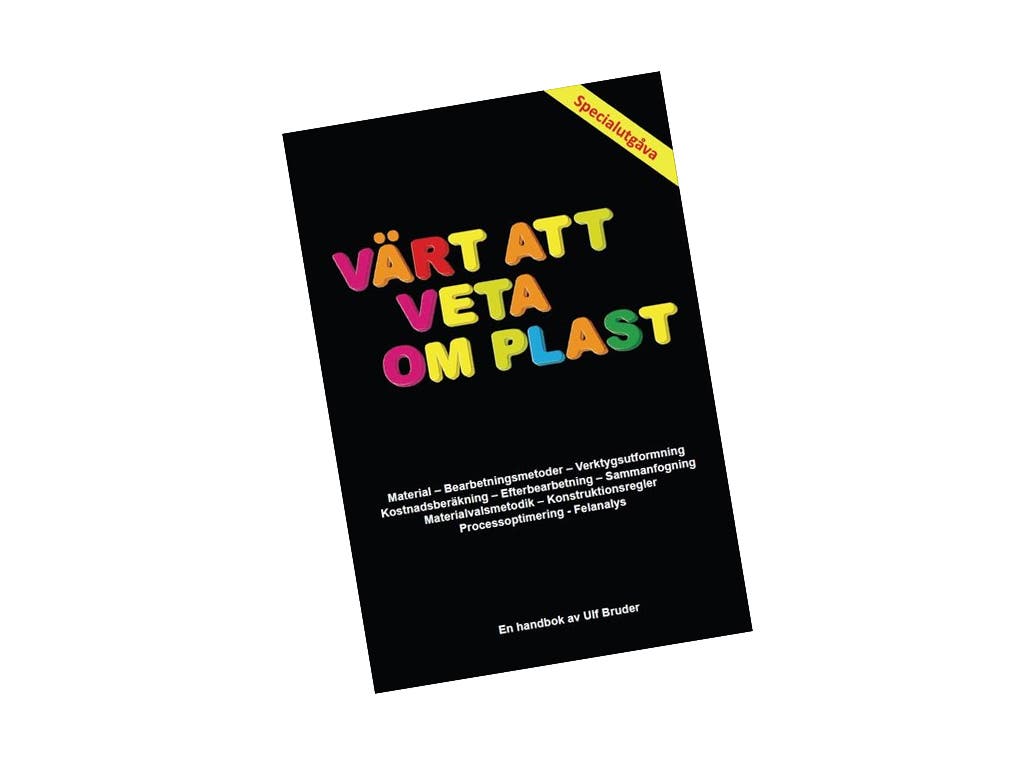
