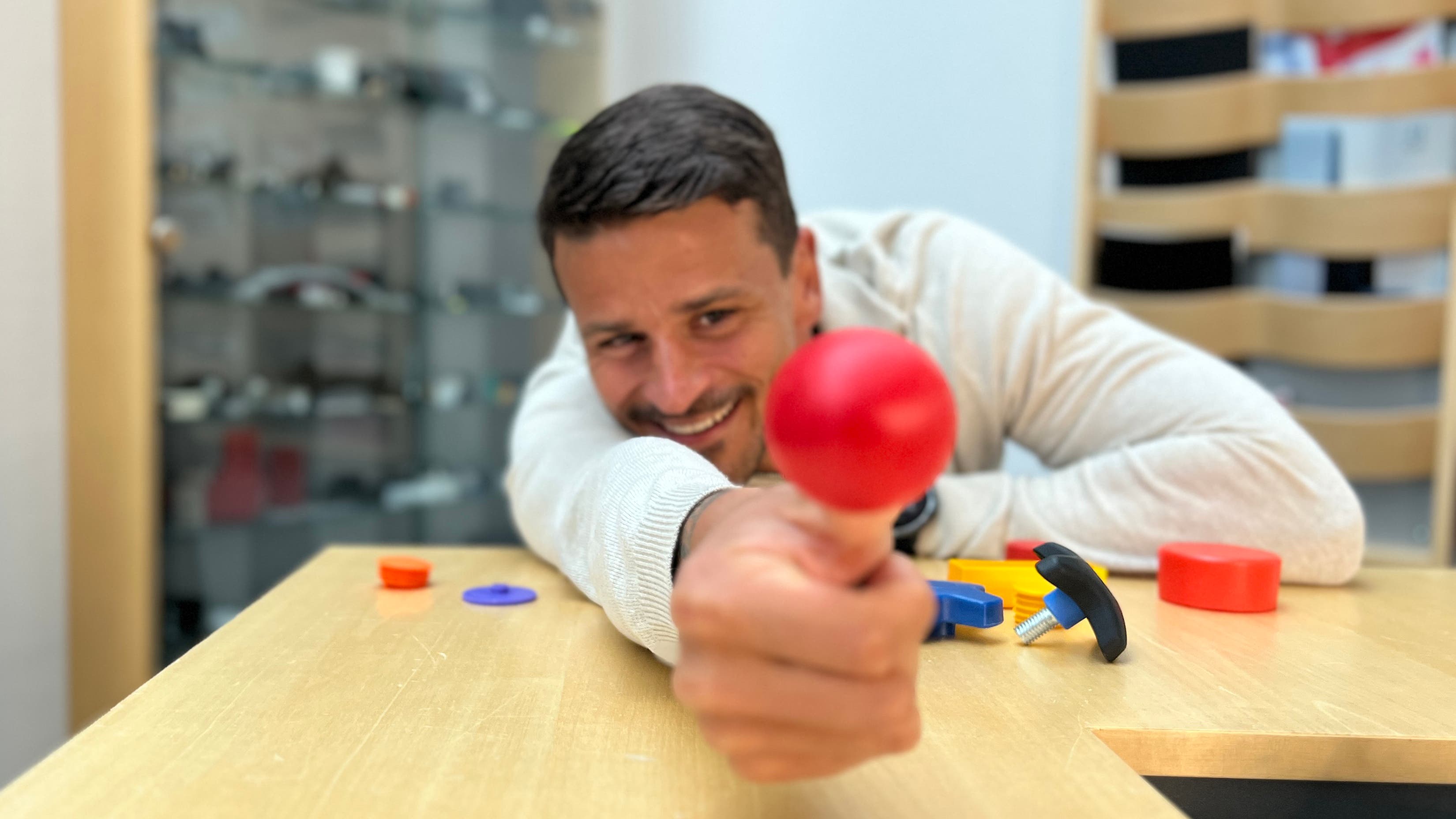
Get help choosing the right one!
Plastic materials for injection molded plastic parts
When it comes to injection molded plastic, the choice of plastic material is crucial for the result. With the right material, you get a longer product lifespan, increased strength, and better resistance to chemicals. If you need to discuss plastic materials,
please contact our product development department.
A selection of the most common
plastic materials we work with
Polyethylene (PE)
Polyethylene is the most common plastic material used in injection molded plastic manufacturing because it is both light and strong. It can be used to create products such as carrying handles, storage bins, and containers. When there are few side branches on the molecule, it gives higher crystallinity, molecular weight, and density. A soft, flexible plastic bag is usually made of LDPE (Low Density) or LLDPE (Linear Low Density), if it is crinkly it may be HDPE (High Density).
Polypropylene (PP)
Polypropylene is another common material that offers high strength and is also resistant to various chemicals and high temperatures. It is often used to create housings and enclosures for electronics and medical devices.
Polyamide (PA) - Nylon
Polyamide is a material that has high mechanical strength and can withstand high temperatures, chemicals, and wear. It is often used to manufacture components in the automotive industry and for portable electronic products such as laptops. Among polyamides, PA6 and PA66 are the most common engineering plastics.
Thermoplastic elastomers (TPE)
These plastics are soft and tough like rubber, have good abrasion resistance, can be made transparent, and are easy to process. Many TPE materials can be cost-effective alternatives to rubber. However, rubber has higher elasticity. TPE is often used on car bumpers as it can be painted or for sports equipment such as fins, snorkels, etc.
Acrylonitrile-butadiene-styrene (ABS)
Acrylonitrile-butadiene-styrene, or ABS, is a material that can provide a smooth and fine surface and is also important for product durability. It is often used to create toys, home electronics, and telecommunications equipment. ABS can be chrome-plated or painted.
Polycarbonate (PC)
PC is a clear and very impact-resistant engineering plastic that is used for CD and DVD discs, but also for shells and visors on motorcycle helmets. PC can be painted.
Acetal/POM
Acetal/POM is the strongest unreinforced plastic and withstands temperatures from -40 to +80 degrees C. It is used in a variety of areas where a material is required to withstand large external stresses such as heat, cold, moisture, abrasion, or for medical applications as it can be sterilized. Acetal/POM is excellent for mechanical post-processing, such as milling, turning, and drilling.
PET
Polyester PET is perhaps best known for being used for recyclable plastic bottles. But it has many properties that make it also used for oven handles, windshield wipers, and irons. PET does not absorb moisture, has good outdoor durability, withstands temperatures up to 155/200 degrees C, and has a high surface gloss, etc. For example, our felt hoods are made of 50% rPET.
Sustainable plastic materials
We continuously test new sustainable materials. Mainly, we work with recycled plastic that we have started using in our standard range, but we also offer biocomposites.
Recycled plastic
Recycled plastic is available in most of the plastic types we work with, such as PE, PP, PA, and POM. The recycled plastic comes from several different sources but for simplicity, it is usually divided into plastic raw material from existing products that have been used and then collected for recycling, so-called PCR (Post Consumer Recycling), and plastic waste generated during an industrial process, also called PIR (Post Industrial Recycling). In the PCR group, we find materials made from old fishing nets and ropes that are fished up from the oceans. With such a material, you kill two birds with one stone by both reducing CO2 emissions and cleaning the oceans.
Biocomposites
Biocomposites are materials made of plastic mixed with natural fibers, such as wood fiber, hemp, or cotton. Today we offer biocomposites with wood fiber that provide an exciting surface, have a lower CO2 footprint, and also smell nice. Here we have the alternatives rPE and rPP.
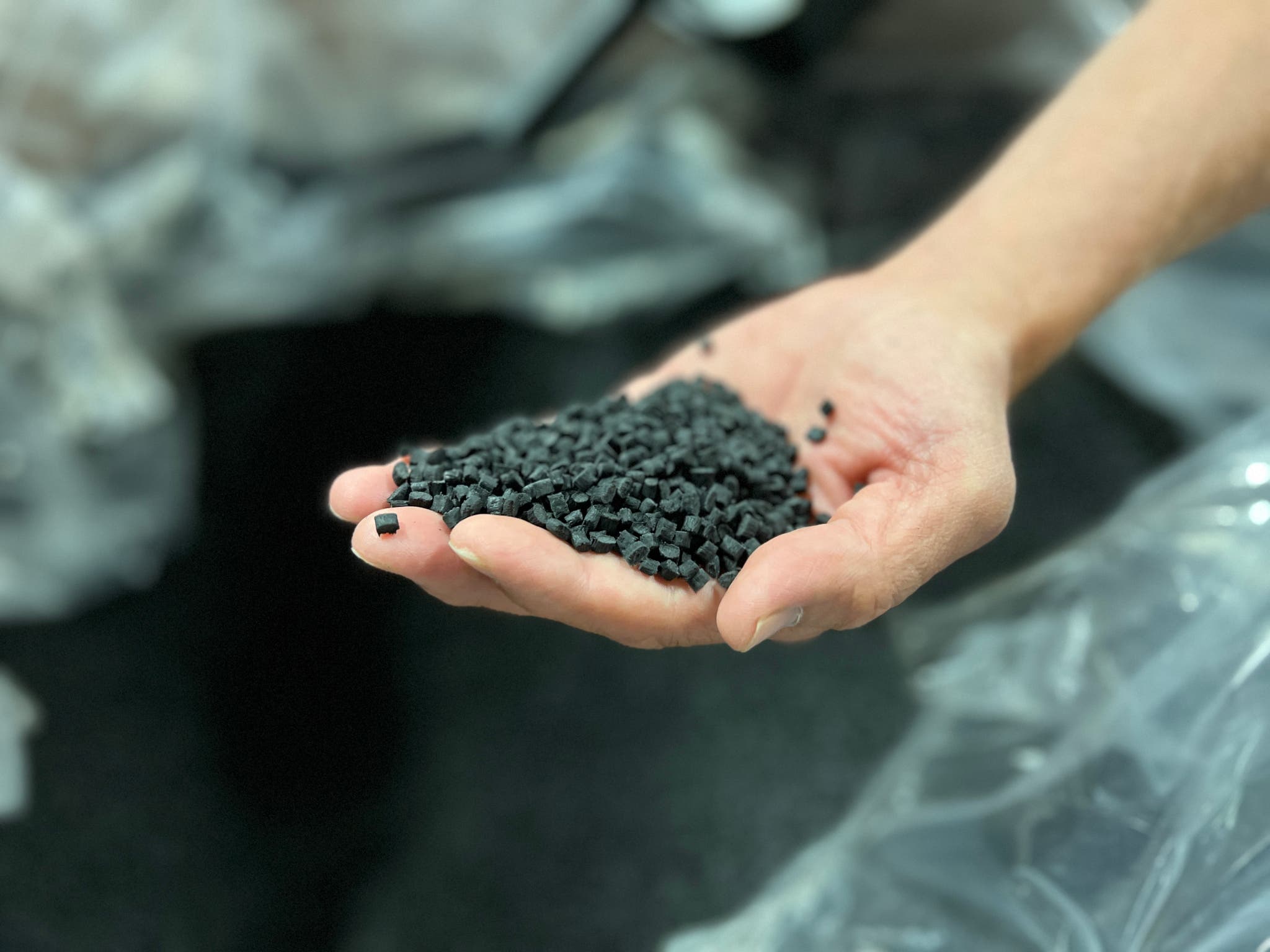
Want to know more about plastic?
Order the book “Worth Knowing About Plastic” from Polymercentrum.
Also available in English.
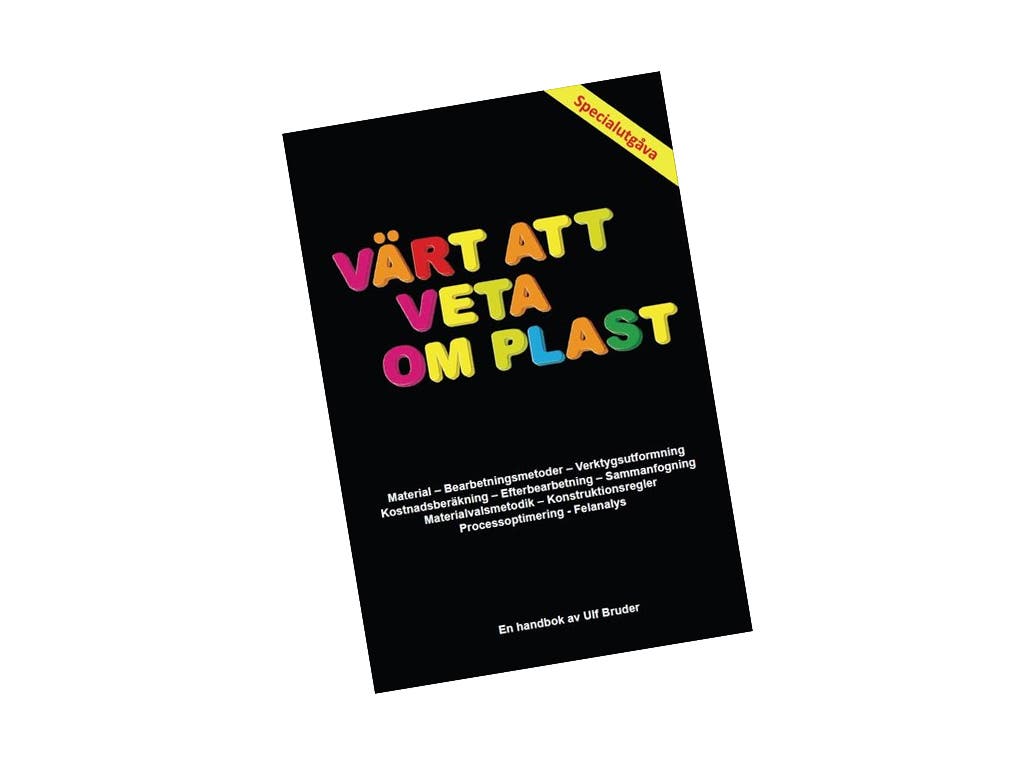
Surface finish and patterns for plastic surfaces
There are many options when it comes to surface finish for injection molded plastic parts. The possibilities are almost endless.
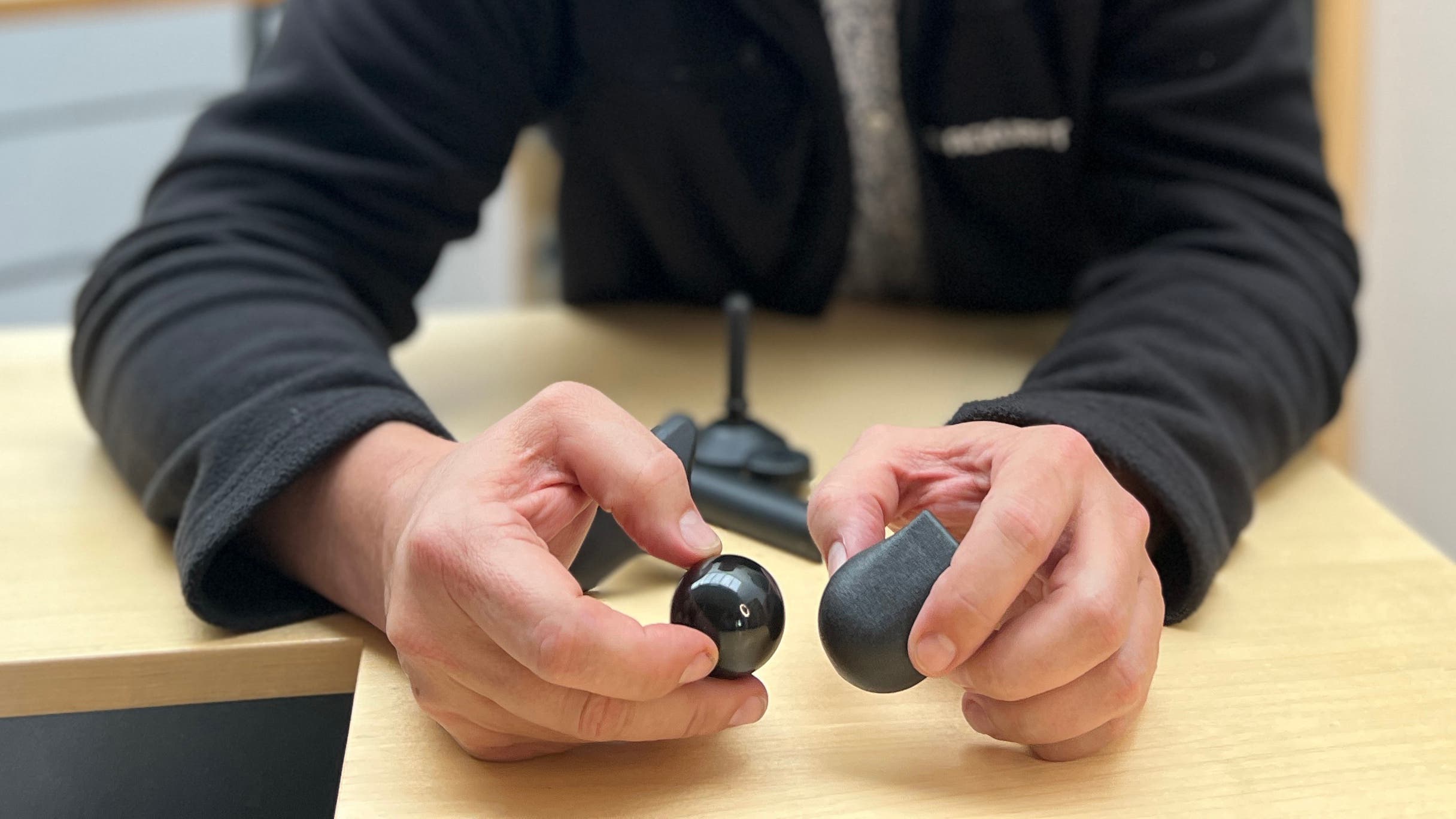
Injection molding - how it works
The production of injection moulded plastic parts requires precisely adjusted machines where our knowledge of the plastic’s properties is very important. Read about how injection moulding works.
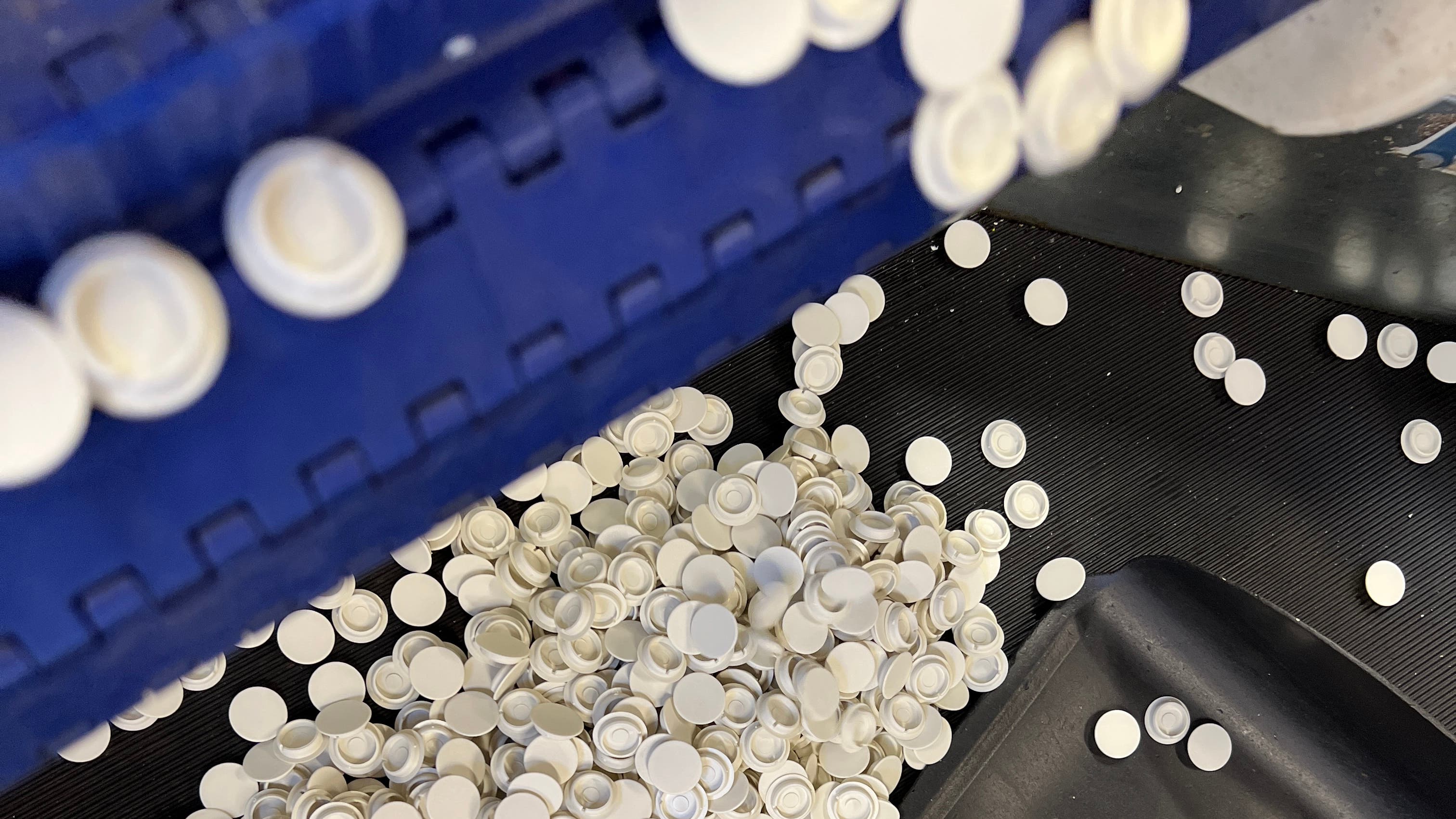
